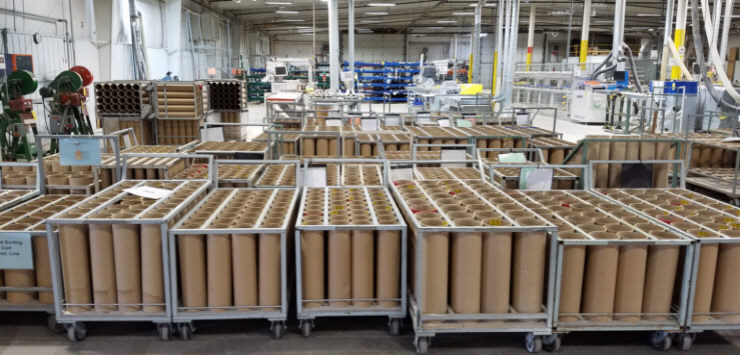
There is only one true measure of improvement in a plant: how much more throughput is produced, while reducing inventory and expenses. And the best way to improve your throughput is by focusing on your bottlenecks and constraints.
The basic premise for this is outlined in our article Theory of Constraints, which is derived from the book
The Goal: A Process of Ongoing Improvement, By Eliyahu Goldratt.
So let's get started on managing you bottlenecks.
What is A Bottleneck?
Bottlenecks (constraints) are anything that inhibit an operation from meeting its goal, which ultimately for businesses is to make money. They can be on the manufacturing floor, in materials, engineering, or anywhere in the system. They are the weakest link in your operation, and they set the pace for your throughput.
Although they may seem the same, a bottleneck and constraint are slightly different. A bottleneck is simply a resource with less capacity than demand, while a constraints are the weakest links in your entire system. All constraints are bottlenecks, but not all bottlenecks are constraints.
For example, if you have an sub-operation in a department that is a bottleneck, but the department as a whole is producing at a higher rate than demand, this bottleneck isn't constraining the whole system. Eventually, however, you will fix the other constraints in your operation, and it will become a limiting factor and thus a constraint. So think of constraints as THE bottleneck of your operation, and is why we use the terms interchangeably in this article.
Also, we are only concerned with long term bottlenecks that are always present in the system, or show up often as your product mix changes. Short term bottleneck events such as a breakdown, absenteeism, or freak snow storm effect throughput, but are one-off events that are not covered by this article.
How Do You Deal With Bottlenecks?
The best way to deal with bottlenecks is to follow the 5 step process outlined in Theory of Constraints. The fives steps are to:
- Identify the Bottleneck
- Elevate the level of performance of the bottleneck using tools you have at hand
- Subordinate all other functions to that bottleneck
- Eliminate the bottleneck
- Move on to the next bottleneck
1) Identify The Bottlenecks
If you have done time studies and know process times throughout your organization, it is easy to spot bottlenecks as they will be present anywhere in the system where production is lower than demand. Unfortunately, this is rarely the case for job shops, and becomes even more problematic for office constraints. Here are some common symptoms:
- Workers in downstream areas constantly complain about waiting
- Area is constantly on overtime
- Piles of Work in Progress (WIP) stacked in front of a process. Be warned that this can also occur when you are over producing in non-bottleneck areas.
- Rush parts or paperwork constantly coming from one department or area
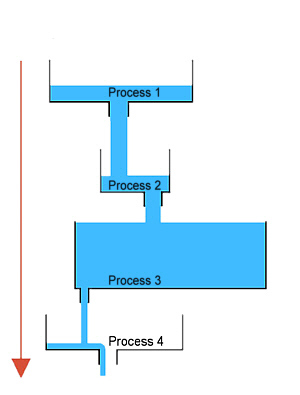
Looking at area efficiency, one department will be running a high efficiency (bottleneck), but the departments following it will have low efficiency because they are being starved for work by the constraint. This is not to say you should be using efficiency by department to run your shop, but it is useful to calculate in this instance
You can also use tools like a fish-bone diagram or a cumulative flow diagram to try to map out potential problem areas.
What Are Some Common Bottlenecks?
Bottlenecks come in variety of different forms, and for job shops they are just as often found in the office as they are on the shop floor.
Equipment
Equipment can be the machinery itself, tooling, or support services, including:
- Not enough machines to do the work, or similarly, they do not run produce enough product to meet demand
- Limited functionality that requires additional processes
- Slow tooling change-over times or setup times of parts
- Not having enough lifting capacity on an overhead crane or fork truck for the product run in an area
- Shared hand tools. I have literally seen a bay of 7 workers all waiting to use the same grinder.
Processes
Some processes are often more time consuming than others. For example, a piece of machinery may be built mechanically in a week, but it may take an additional week to wire and install automation.
People
People can be broken down further into:
- Total Number of people in an area
- Training, or more often the lack of cross training, can create huge bottlenecks
- Shop floor attitudes, particularly "This is the way we have always done"
Materials
It is often a great challenge to coordinate material delivery to a production schedule that is constantly changing, thus:
- Materials group is under-staffed or inefficient, and cannot keep up with demand
- Long lead-time materials or parts are consistently late, causing a chain reaction where other jobs are pulled up, causing even more material shortages down the road. Recent US Tariffs on Chinese steel caused long lean times and created bottlenecks for many US job shops is an example.
- Fasteners and other small parts are ordered by a batch system that does not replenish fast enough
Programming
Programming for CNC machines or robots is often centralized in the office, and as the complexity and size of the plant increases, so does the potential for a bottleneck.
Engineering/Drafting
For custom engineered products, engineering and drafting is almost always a bottleneck eventually as production outpaces their ability to convert customer specifications into usable drawings
Information
The flow and accuracy of information to the shop floor is a common job shop bottleneck, particularly in a mufti-shift operation where there is no office support beyond first shift. These include:
- Customer specifications
- Bills of materials
- Material cuttings
- Shipping paperwork
- Priorities
- Not having an efficient scheduling system that addresses bottlenecks will create actually create additional bottlenecks, both in the office, plant, and with vendors
Quality
Quality constraints arise from both production and quality departments:
- Consistently bad production quality from a machine that requires rework
- Waiting for quality inspectors to arrive and complete their work
Policy
Policy bottlenecks come in many forms, including:
- Internal plant policies or procedures that inhibit production
- Customer specifications
- Union contracts
- ISO, ASTM, AWS, or other outside sanctioning organization rules
- OSHA, EPA, FDA, or other government regulatory agency rules
Market
Market refers to producing more than your marketing can sell, which will only come into play if you make some stock items. Most job shops will have orders associated with their production. However, one common area where a job shop will carry finished goods inventory which is for spare parts, which must be managed like any inventory
2) Elevate Bottlenecks
A simple definition for the Elevate phase is this: "Maximize production through a bottleneck with what you have at hand." These can be done very quickly and should require little investment. This sounds easy enough, so what are some common ways to achieve this?
Job shops often run a mix of products through their plants where they don't use all processes all the time. Their backlogs consist of a similar amount of hours, but those hours are divided between different operational areas each month. If one learns how to properly schedule around your constraints using
mix charts, you may be able to schedule a bottleneck out of existence. For example, if you know next week you will be over capacity on a machine, pull the portion of those jobs that run through that machine up earlier when the machine is not running. Institute a rolling frozen schedule for that machine so that it is not constantly changing jobs and losing efficiency. For example, lock in the schedule on that machine for 3 days, and new work can only be added to it's schedule after that. This can only be overridden by the plant manager.
Adjust worker schedules so that processes are not idle during breaks or lunch. Also, you may be able to stagger shifts so that workers come in early to stay late (on straight time) to give extra time on the machine. Obviously overtime for the constraint only is also an option.
Cross train additional workers to the process so it is never idle due to absenteeism.
Make the constraint a priority of management and ensure it is constantly monitored. Keeping constant pressure on the constraint will generally lead to some gains in throughput.
Look to shift some of the work load from the constraint area to other areas.
Create a "buffer" for the constraint so it doesn't run out of work, as detailed in Drum Buffer Rope.
Shift people from non-constraint areas to the constraint, so long as you gain additional output through the constraint by doing so. A common complaint you will hear to this approach from senior plant leadership is that the additional people may not be working at 100% efficiency. This is very short sighted, because you are essentially trading a little department efficiency to improve your overall plant efficiency, which I detail in a later article about Treating Efficiency As A Currency.
For automated process constraints, develop a side branch to the value stream that duplicates the function of the automation, using manual labor. Undoubtedly this will not be as efficient as the automation but again be willing to sacrifice a little local efficiency if it increase overall throughput.
Add an additional shift on ONLY the constraint area, or work overtime in that area.
Outsourcing part of the constraint should be your last option, but don't take it off the table completely as it is still far better than slowing down your entire plant over one operation.
Look through the ideas presented later in this article as their can be a lot of overlap between the opportunities in the elevate and eliminate phases.
3) Subordinate All Other Functions to that Bottleneck
Quite simply, the bottleneck becomes the focus of your operation, and all other work is reorganized around the bottleneck. This means:
- The Bottleneck has work scheduled through it 100% of the time, while other areas in the value stream will not always be operational.
- It is always fully staffed, with labor being drawn from the non-constraint areas when needed.
- It receives priority attention from maintenance, material handlers, and any other support staff.
One final method used to subordinate other functions to the bottleneck is through the use of a Drum Buffer Rope system. A Drum Buffer Rope basically is a system of WIP management that provides a sufficient buffer of raw material for the bottleneck so that it is never effected by shortages. The discussion of this system is beyond the scope of this article, and tackled in our article Drum Buffer Rope.
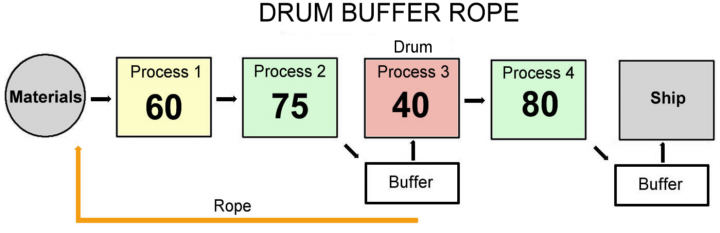
4) Eliminate Bottlenecks
The name is self explanatory: Eliminate the bottleneck from your operation permanently. The eliminate phase differs from the elevate phase in this way; elevating solutions are generally immediate and low cost, while eliminating solutions generally require redesigning your value stream and possibly capital investments.
The most obvious solution is to buy more equipment and capacity for the bottleneck operation, but this really should be the last option as there are often ways to "engineer the bottleneck out" without capital spending. These include:
Completely redesign the process from scratch. Often our processes started out simple but over time more and more "bloat" was added to them, making them inefficient. Be willing to start from scratch, and re-evaluate the layout and steps of the process.
Minimize downtime for tool and die change-over, or to setup a work station. This is one of the biggest wastes found in job shops as you are constantly switching your setups between jobs. Single Minute Exchange of Dies (SMED), flexible work stations, other systems that speed up the change-over process are often enough to eliminate a bottleneck.
Material handling is another huge waste. Add conveyors, overhead cranes, lifting devices, and anything else that will speed up material handling both internal and external to the constraint.
Break apart the process into multiple processes with a shorter process time, so it is no longer a bottleneck. For example, if a worker is required to debur parts coming off a CNC machine, transfer that responsibility to the next step in the process if that is not a bottleneck. This is also very applicable to office functions, where you can remove some of work from one overworked person and transfer it to another.
Organize parts, raw material, and information going into the process in a manner that makes it easier to consume. For example, if an assembly process is slowing you down, deliver all the parts to this station, stacked in the order they are needed, and remove any packaging that might slow them down.
Add or reassign someone to be a dedicated material handler for the bottleneck.
Equipment downtime is another common constraint. Institute a Total Productive Maintenance (TPM) program, focused mainly on your constraints. This can bring your equipment up to "like-new" status, and keep it that way.
For an office function, go through every single report and piece of paperwork they do. Anything non-essential get shifted to another functional area, or ended outright. Office functions often "collect" reports or paperwork that are time consuming, yet no one really needs or uses the data.
For drafting functions, try reuse as many drawings as possible, and only render what the shop actually needs. Many drawing packets end up with numerous drawings that aren't useful to the shop floor, simply because no one asked.
Probably the most difficult bottleneck to overcome is the labor market; you simply cannot find enough qualified people in your immediate area. Automation is usually not a viable solution due to the nature of job shops. Higher wages can attract more labor (assuming they don't price your company out of your market), but often the problem is not the quantity of labor but the skills available in your labor pool. One solution is to "dumb-down" processes so the skills needed are minimized. However, ultimately you may end up having to institute an extensive training program or even an internal school to "build" your ideal employee from the existing candidate pool.
5) Move on to the Next Bottleneck
The final step in the bottleneck removal process as outline in the Theory of Constraints is to move on to the next constraint. While this sounds straight forward, it is often more complicated than most realize.
You simply do not drop down to the next constraint on an ordered list and begin work. You literally have "resuffled the deck" in your organization, and will need to start the complete process over from scratch. New constraints will emmerge where there were none before, and old constraints may disappear. You also need to be aware that removing constraints creates a momentum similar to a dam breaking that can also cause all kinds of unintended issues.
For example, in a previous assignment of mine, we removed a major constraint in the front end of the plant, which jumped department efficiency from 88% to 107%, and rose overall plant efficiency to 103%. The departments downstream could handle the additional production, and everything was great for about 2 months. Then we started to run out of raw materials because our materials group did not have the systems in place to handle the additional capacity, engineering could not provide us drawings fast enough, and we literally ran the plant out of work.
The situation described previously is not an outlier, but is actually the norm once bottlenecks are eliminated. The new constraints that emerge will be unique in each plant, even if you have multiple plants running identical product in your organization. So before you go live with your new systems be aware of how your system as a whole will react, and try to predict where your potential issues will be.
Conclusions
You could write a unique book on removing bottlenecks in every manufacturing facility in the world, but hopefully this article provides a good primer to getting you started. Feel free to add your experiences or questions below. I'd love to hear how you elminted bottlenecks from your operation, or any additional questions you may have.