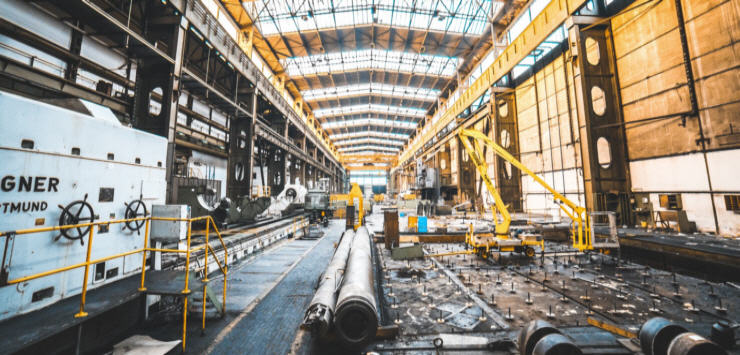
Drum Buffer is a key scheduling component of the Theory of Constraints for managing constraints. If you have not already done, please check out our companion articles to this on the topic of Theory of Constraints:
What is Drum Buffer Rope
Drum Buffer Rope refers to a replenishment scheduling system develop in the book
The Goal: A Process of Ongoing Improvement,
by Eliyahu Goldratt.
In the book, the story's protagonist was on a group field trip with his son, hiking on wood trails. Because of vast differences in walking speed, the group kept getting spread apart. He developed a system where he tied the kids together with a rope so they walked at the same speed, paced by the slowest walker.
In the real world, the drum refers to the speed with which product moves through a constraint, which will be the slowest process. Think of a drummer beating a cadence to which others march. The buffer refers to a small amount of managed WIP in front the constraint, which accomplishes two things: control the amount of WIP produced to avoid overproduction, and to make sure that the constraint is not interrupted due to lack of law materials. The final element is the rope, which refers to a signal used within the process to notify preceding process that the buffer is getting low and needs to be replenished. Graphically, drum buffer rope looks like:
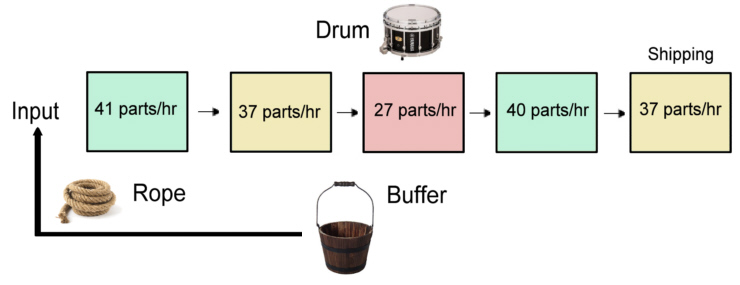
The plant can ship 37 parts/hr, so as your can see, the middle process is a constraint at 27 parts/hr. If left unchecked, WIP would pile up in front of this process as the two proceeding process can produce at a much accelerated rate. We use the buffer and rope mechanism to control WIP, and send a message to the input of the area to replenish the buffer.
Drum Buffer Rope In Practice
The previous example is pretty standard and similar to what you will find in any Theory of Constraints course. But what does it look like in practice in a job shop? The reality can look much different. Here is a scenario from my consulting work:
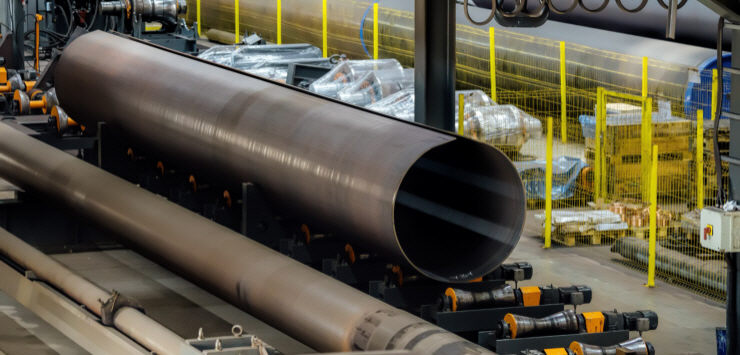
A metal manufacturer that made large steel pipe products that were custom sizes and configurations. Most of these were custom engineered and One of their constraints was in the front end of the plant where they formed the pipes. Sheet steel was brought into the plant, laser cut to size, rolled into shape, and then run through a machine that welded a seam down the length of them. The value stream actually had a branch in it as well, based upon the size of product. This example covered the large product branch, and shows production over an 8 hour shift.
![]()
There are a number of issues that make this scenario challenging:
The Drum in this case is actually two processes, which were level loaded to have the same output. They involved tacking pieces together, then welding the seam on them.
Instead of having the buffer right in front of the drum, the buffer is actually before the previous process, the rolling process. This had to be done because of space constraints near the drum processes. The rolling process was controlled by only partially staffing it to prevent overproduction
The buffer was 8 sections, which was one shifts worth of production for the constraint
The rope sent a returned cutting to the materials group, which released another batch of 8 sheets of steel.
As if this wasn't complicated enough, there is actually a second constraint to deal with in this situation.
Under a certain size, production is shifted to the smaller branch of the value stream, and then the constraints shifts to the laser cutting operation. So when running large product the cutting table is subjected to the seaming processes, but when running small product every is subjugated to it
Just like with the other value stream, the cutting table has a buffer as well. Actually, it has 3 buffers - one for steel, one for paperwork, one for programs
So as you can see, real world application of a drum buffer rope can become very complex. Despite the complexity, it is still an invaluable tool for controlling WIP in a job shop, and making sure your constraints are always fed with raw materials. Drum Buffer Rope setups are key components of the elevate and subjugate phases of the Theory of Constraints.