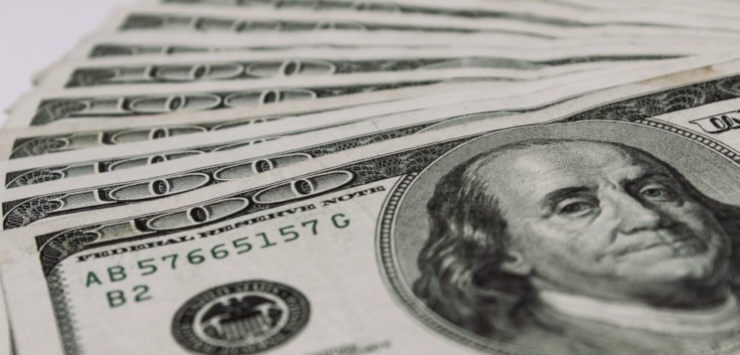
It ain't what you don't know that gets you into trouble. It's what you know for sure that just ain't so.
- Falsely attributed to Mark Twain
We all have beliefs that we are sure are correct, only to find out later in life how wrong we really were. Some of those beliefs for me revolved around how efficiency works in a job shop, which have changed immensely as I have grown as a leader. I now treat efficiency in my plants as a currency, which is to be spent and saved accordingly.
Tracking Labor Efficiency By Department
There are three closely related behaviors which are extremely detrimental to the overall efficiency of your operation. They are:
I need to track efficiency by department to get the most out of my plant
This is almost universally done throughout manufacturing, but I must caution that it is a very dangerous practice in a job shop. You should measure it to understand what is happening in an area, and where opportunities exist. You should not, however, make it a goal unto itself as it breeds a lot of very bad behaviors, particularly the next two items.
I Need To Keep Every Piece of Equipment Running all The Time
If you have this mindset, stop immediately. No seriously, purge this nonsense out of you mind this instant. This philosophy only works when all of your processes are level-loaded and all equipment is needed all the time. In a high variation low run job shop environment that simply is not the case. We should treat our equipment and processes like a salad bar, picking and choosing what we need for a particular product.
This philosophy is usually driven by those who want to see a return on investment for equipment, usually in some unrealistic time frame. Our decision making needs to be driven by what will make us more profitable, not artificial constraints.
I Should Only Run Product Through The Most Efficient Processes
The mindset on this one is "I have this big fancy new machine that is much more efficient than the old way and should ONLY run product on it". Eventually you come to a point where the new machine can't keep up, work piles up behind it, and you've created an artificial constraint because of stubbornness.
So why are these bad?
First, they drive us to not properly allocate resources where they are needed. Instead of shifting around our labor and other resources to the constraints dictated by your current mix of product, you allocate resources based on an artificial need to keep everyone busy. Job shops are a like a game of Tetris, and you should be constantly moving your pieces around to where they fit best.
Second, they build a great deal of WIP. Because we are not properly allocating resources, we tend to work ahead on future jobs creating piles of inventory that get damaged/lost, take up floor space, and ultimately tie up money.
Third, they ultimately cost us plant efficiency. By not shifting plant resources where they are needed, and by artificially keeping areas busy, we are creating artificial constraints.
Also, look at the behaviors you are reinforcing here. Workers see all the WIP they are creating, have no where to put more product, and slow down. Conversely, as you struggle to keep the machines in work, they don't see much work in front of them, so they slow down to make what they have last. See a pattern here?
Treat Efficiency as A Currency
You need to take a different approach to your efficiency. I suggest treating it as a currency. With currency, more is always better. Likewise, no one will ever complain about being too efficient. We don't like it when are bills get too high, nor do we like it when our efficiency drops. Sometimes we need to spend money to make even more money, like we do when we invest. You need to be willing to do the same with your efficiency. Here are some examples:
Transfer Labor Between Departments
You need to be tracking your labor hours through each work area, and know the capacity at each work station. When the work hours is less than the capacity, labor should be shifted to other areas, or work transferred from overburdened processes if possible. The opposite it true when there is too much work. Each work station should be staffed and loaded for 100% efficiency, or not all. This is the equivalent of turning lights off when you are not in the room to cut down on your electric bill.
When I was in the custom engineered utility structure business, I used to track capacity and work by station and shift, and communicate to the supervisors where they excess labor and where they needed more. I then had them put together a plan on how they were going to shift their people or work, we reviewed it together, made changes as necessary, and then executed it. This not only improved plant efficiency but also greatly improved the velocity at which work moved through the plant.
This also highlights the needed for cross-training and to have a robust production planning system based on hours, which we detail in a later articles.
Throw Labor at Constraints
Be willing to spend your department efficiency on overall plant efficiency. It's okay to "throw" labor at a process so long as that process is a constraint and the extra labor will help free that constraint. Here is an example from my past:
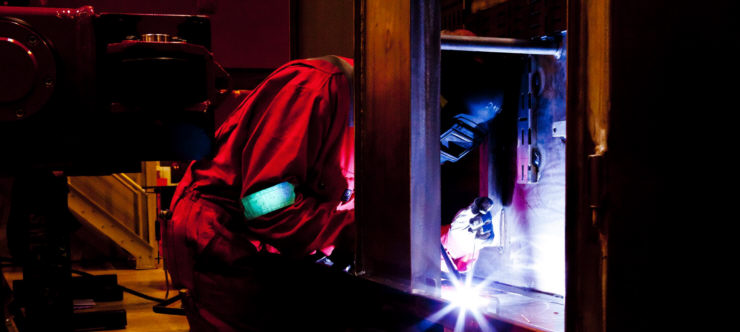
A small military contractor had a robot welder that welded together expanded steel doors. The process was the primary constraint for the operation. The owner was very almost hostile when I suggested adding more labor to it. The machine was twice as fast as a human welder, and he thought there was no way "wasting" labor on it would help the flow.
Eventually he allowed us to run a trial. We broke up duties on the robot welder between two people (one on each side of the machine) to reduce motion waste, and reworked processes before and after so that these two had just the right amount of work. We also added a parallel station where two people manually fabricated these doors for half of the shift. Essentially, we were doing the "elevate" stage in the theory of constraints.
The results were startling. With this major constraint freed, WIP in the back of the shop plummeted, the workers finishing the product could barely keep up, and overall output of the plant jumped by 20%. Yet if you measured the efficiency on just that machine or in that department, it would look atrocious. In a longer term view, you eventually would justify a second machine improve this.
As you can see, there are some pretty compelling reasons to re-evaluate how you treat efficiency in your plant, and develop your own system to use it as a currency. Be willing to move and spend this valuable currency where it is needed, even if it makes certain areas of your operation less efficient.