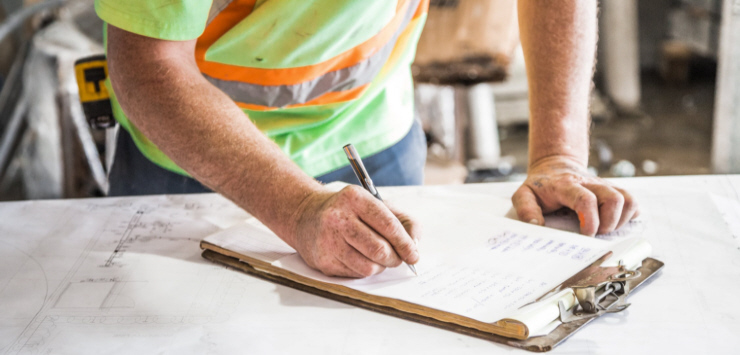
Like so many other tasks, the variability of work in a job shop can pose a number of challenges when trying to write Job Safety Analysis (JSA) documents and procedures in your plant. You never know where new exposures will arise as processes, people, and products change. Thankfully we can apply some of the lessons learned from increasing productivity to safety as well.
What is a Job Safety Analysis?
A job safety analysis (also known as Job Hazard Analysis) is a step-by-step description of all the functions performed in a job. It is essentially a risk assessment. At each step, possible safety or health hazards are identified, as are the controls used to minimize the risk of injury. These can include PPE, Lock-Out Tag-Out, confined space protocols, or even best-practices. In a perfect world, you would have a JSA for each job in your plant, and have all exposed employees trained to it.
The problem arises in that jobs shops often must re-invent themselves with each product they produce. New processes, procedures, tooling, and people are introduced into the workplace on a daily basis, making it extremely difficult to build safety procedures that cover all potential present or future exposures. To make matters worse, the jobs themselves make an injury more likely because the workers may not see or understand the potential exposures.
How To Create A JSA
JSA's are produced by following these basic steps:
1) Choose A Job
While it would be ideal to have a JSA for everything anyone could possibly do in your job shop, that simply isn't possible. In fact, jobs may only exist for one product, then disappear entirely. We need to take a different approach.
Break down Jobs Into Sub-Processes
Much like we did when creating standard work, break down jobs into small sub-processes. We won't make a JSA for building a complete machine, but will have a number of them from building the frame, assembling parts, wiring, and testing. Keep the number of steps in each process small. Then just like a salad bar, when workers pick and choose which processes are needed, most of their actions will be covered by multiple JSA.Divide Jobs in Product Classes
Sometimes we can divide by the type of product being run. Even though each product may all be slightly different, they may be similar enough so that some general safety rules apply.Choose jobs based on shared hazards
Sometimes products or even jobs may have absolutely nothing to do with each other, but they may have a shared hazard. A common one is to develop rules for jobs where there are pinch points for finger or other extremities.High Risk
Sometimes you will have to bite the bullet and write a number of job-specific Job Safety Observations because a serious injury occurred or because of the risk of one occurring is great. The same is true if you have OSHA violations in this area in the past.2) Break down each process into the key steps.
This is where a background in Training Within Industry (TWI) really is useful. Just like processes are broken down for training purposes, they can also be broken down into simple steps that make effect JSA documents. It seems like a tedious process, but in the end is absolutely required to be effective.But don't write these sitting in an office. You need to be in the Gemba (shop floor) watching the process being performed and interact with the workers. Ask them what different variations of the process exists, and of additional hazards that sometimes come into play. Much like standard work is produced by the workers, so should JSA steps.
3) Determine the Hazards
This is where your expertise as a safety professional comes in to play. You need to identify the potential hazards at each step of the process, and the area hazards. While the former is relatively straight forward, the latter can be difficult in an environment in flux. This is why it is critical to stay engaged with the workers, and find out how their environment changes over time to anticipate future hazards.The most common hazards that can occur in this changing environment often come from material handling and pinch hazards. Most people are creatures of habit, and falling into a sense of complacency is dangerous when moving materials in a changing environment. Pinch points are more common because workers may not know the dynamics of a product or process that is new, and no safety control are available or in place.
Once you have the hazards, you will want to use a risk matrix to determine the likelihood of injury. You will need to evaluate the severity potential of injuries, and the likelihood of them occurring. Check out our article on how to create a risk matrix for more details (coming soon).
4) Identify Controls
This also become a difficult task because of the changing environment. Many of the controls commonly used such as guarding will not be available for one-off or short run processes.
Keep it simple, and start with general PPE. You may want to up your general requirement to cover potential future hazards. For example, you may wish to require steel toe boots that have both metatarsal crush protection and electric protection for shock hazards for everyone, even if most of the time most of your work force does not need it. You may also require that everywhere cotton t-shirts with no silk screening as an arc flash protection.
Eliminating hazards are going to be very difficult in this environment, so much will have to be done with administrative controls. Keep the controls narrow in scope to a single process, but have more controls.
Aside from individual process procedures, you may wish to require that certain aspects of work being inspected by a manager or safety professional before work proceeds. This is particularly true of jobs that have been determined to be high risk.
Don't wait to consult safety until a new product type hits the shop floor - do it in the planning phase. Engineering and production management will often have better visibility to future work, and the potential hazards they pose. Including safety in the early stages of production planning allow them time to react, build controls, and train the workforce before product hits the floor.