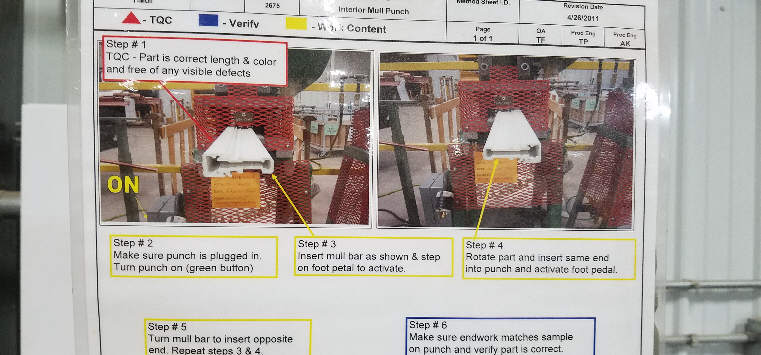
There is a common misconception in industry that standard work doesn't apply to job shops or made-to-order operations because the product is always different. Nothing could be further from the truth. It is very applicable in low-volume high-variation environments, but like so many other lean tools it just looks different. In fact, I would say it is one of the most important tools you can use to improve and maintain your productivity.
What is Standard Work?
Standard work is simply the best practices work sequence for a job. It is the most efficient path to creating value for the customer. Standard work creates a baseline for performance, and it should change over time as tooling, quality, and processes improve over time.
It is important to note that standard work is not some standardized process developed by executives and enforced on the work force. It is also more than a work instruction. Standard work is the best practices (currently) to do a job. It is owned and developed by the people doing the work, based on the needs of the customer.
Standard work is ultimately not for the worker; they already know how to do the job. Standard work is for management to understand if a process is in control and operating properly. That is why at Toyota standard work documents face out towards the isle instead of towards the worker.
Standard Work Vs TWI
There is sometimes some confusion between standard work vs Training Within Industry (TWI). Standardized work is the sequence of tasks, while TWI is the process of identifying the key steps of the process and following a sequence that simplifies the training process. Standard work creates uniformity in your processes across your plant, while TWI simplifies and increases the speed with which people can be trained. The two do have some shared concepts, and in fact Toyota's Job Element Sheets were derived from TWI Job breakdown sheet.
For our purposes, we are going to use concepts from both.
Benefits
The benefits of standard work include:
- Creates process ownership; the process was created by the workers, so they feel engaged in the process and work in general.
- Insures work is always done to the current best practices, which increases productivity and safety. You might be shocked by just how much that is. I have observed a 20% increase in efficiency by simply creating standard work on how to handle scrap off a process.
- Improve product consistency, which improves overall product quality and customer satisfaction.
- Removes common errors and reduces reject rates increases internal quality
- Increase the accuracy of the job estimation process
- Process productivity and quality become repeatable between work stations, shifts, and even plants.
Where Do You Start?
This is first question one must answer, and it is also the easiest. If you have read any of my other articles on job shop lean, you already know the answer. Standard work should be applied to your plant's bottlenecks and constraints via the theory of constraints process. For more information, read my article on The Theory of Constraints.
What Processes Lend Themselves To Standard Work in A Job Shop
A first myth that should be dispelled is that you have to create a long piece of standard work for each product you run. Not only is this inefficient, but probably not even realistically possible when you constant change your product. We will not be creating standard work for products in most cases, but instead for individual processes.
Think of your job shop giant salad bar. With each product you produce, you pick and choose the items off the salad bar you need to use to build it. Some salads may have croutons and bacon, others cottage cheese, and almost all have some different salad dressing. So we will build standard work to handle as many of the items on the salad bar as we can, then combine them into the finished product. Because of the variation in products, not every process step will have standard work, but the common ones will. For example, if you were doing custom machining, the machine process itself may not have standard work. However, there are many sub processes that will occur every time regardless of the product run, which could include:
- Acquiring raw material
- Fastening parts within a machine
- Load the correct program
- Edge finding on the part
- Unloading
- Marking
- Scrap Handing
You get the picture. Even though you are always running different product, there are always a number of steps that always occur regardless of what is being produced.
Steps To Implementing Standard Work
Identify the constraint you will attempt to eliminate through standard work through the theory of constraints process and build a team to tackle it. It should consist of (at a bare minimum) workers on the process, one of the leaders over the process, and a representative from the next process. You may also wish to have maintenance, safety, and quality represented as well.
Break down big processes into the smallest possible sub processes possible. Observe the work and involve the stakeholders (workers doing the work) in this process. Do time studies to see how long each step actually takes. This is where TWI comes into play, and does a wonderful job of helping to break down things into manageable chunks. Once you narrow the process down to a manageable size that you would feel comfortable doing TWI training on, that is the ideal size for standard work.
For example, on the process of running a cutting table, you may want to break that process down into loading raw material, setting up the program, consumable changes, off-loading finished product, and scrap handling.
We would create standard work all these process to reduce the overall process time.
Determine what success will mean, or our in our case, at what rate we will need to produce so that the process is no longer a constraint. You will need to calculate:
Takt time, or the available time for the process / demand of the next process. Keep in mind, tact time may change if your routings change because demand will change at the next process. You may want to take the worst case scenario for takt time (next process with the most demand) so that you know the constraint is truly removed
Total cycle time for the process, and all the sub process times. The total process time will vary, so you may wish to break down the process time into "classes" of products and use an average. For example, in our cutting table example, we may wish to break into down by thickness of product cut or size by area, whatever makes sense in your business
Determine all the steps in the process, and sequence of those steps. Eliminate obvious waste from the process. In particular motion, waiting, and excessive processing show up a lot in standard work events.
Determine how much Work in Process or Progress (WIP) should be associated with it. In particular, if this is a constraint you may wish to have a drum buffer rope system in place for it.
Determine what the ideal new process will look like, and do "dry run" time studies to determine realistically what the new standard process will produce. Keep in mind, the new takt time may still not completely meet customer demand, but it should get you much closer to where you need to be. You will then need to apply other tools to completely eliminate the constraint.
Document, Train everyone to the new standard work process, and audit it regularly. Inspect what you expect. If you don't audit for compliance, it will slip back to the way it was before, and you would have been better to not do the event at all.
Wrapping It Up
Standard Work can be a powerful tool to improve the efficiency, create consistency between operators, and keep processes in control. It has a unique implementation in job shop environments, but nonetheless is invaluable.