
Have you ever implemented a lean improvement in your job shop that should have made a substantial difference in your companies bottom line, only to see negligible or even negative effects instead? This is an extremely common problem, and often leads companies and workers alike to the erroneous conclusion that lean doesn't work in Job Shop environments.
The problem isn't the improvements made, but with the flawed methodology used to choose the location of where to start, and a lack of understanding of the labor dynamics of a low volume high variation environment. So let's start out by analyzing the causes.
How Lean Implementation Areas Are Chosen
Most lean Kaizen events are chosen chosen using some variation of the following:
Value Stream Map
Many consultants are guilty of this one because they do not truly understand the dynamics of a job shop. The thought process is to create a value stream map of the entire operation, then look for the opportunities. The problem is job shops often have a constantly changing mix of work that varies in process time and possibly in the processes used. Any Value Stream Map created may only be valid for a very short period of time, so what looks like a great opportunity today will not make sense tomorrow.
Easy to Implement
The thought process is this: hold a Kaizen event in an area with some supposed "low hanging fruit" problem that can be easily solved, thus introducing your work force to lean principals while making some tangible gains. Almost all operations do this at some point, and while it does make a lot of sense from the standpoint of building a lean culture, expectations needs to be tempered. Very rarely will you see gains that will be seen to the bottle line of the plant, and these types of events almost never transform a business. It is also important to understand the cultural dynamic you are reinforcing with this:
"Lean changes were made, yet no significant changes to our business or bottom line can be seen. Thus lean doesn't work in a job shop."
Regardless if this is true or not, this will be the perception of what occurred. So if you choose to go this route, I suggest sticking to 5S events in "messy" areas of the plant. People can get their feet wet in the process, the need is obvious, and it can be sold as a housekeeping, safety, or quality of work life event.
Largest Area of The Plant
Usually chosen by the number of people in a department, the thought process is this:
"More People = More Hours of Labor = Greatest Opportunity To Make An Impact"
The logic is sound, but one major flaw exists: you will never see these improvements while constraints in other areas of your plant exist. Period. Not one point of efficiency, not one extra unit shipped. All you will do is either create WIP, or drain efficiency, the reasons for which I detail in the next section.
Don't believe me? Look at the graphic below, which is a common visualization of work flowing through your plant. If I make the valve on process 4 bigger, how much extra water flows through the system? The answer is none, not a single drop more flows through the system. If you haven't done so already, I strongly encourage you to read our articles on Theory of Constraints and bottlenecks.
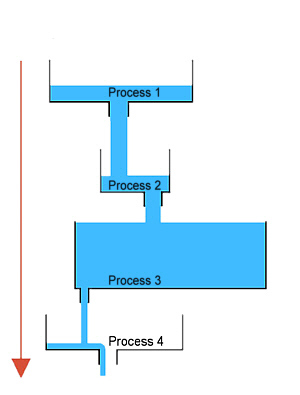
Bottleneck, But Not a Constraint
This one afflicts beginning and seasoned practitioners alike, often from a misunderstanding of the flow of work. Bottlenecks and Constraints are not necessarily the same thing. Constraints are always bottlenecks, but bottlenecks are not always constraints.
A constraint is something that affects the flow of product through your entire system, and is always present. It is THE bottleneck for your entire plant. EVERY plant has them. A bottleneck effects flow of product at one point. In a job shop, the mix constantly changes and not all resources are needed all the time. Thus, even though something is a bottleneck in a debarment doesn't mean it will affect the overall flow of product through the plant. There will be periods where work backs up and delays occur, but as the mix changes the demand diminishes the bottleneck goes away. This is why it is critical to address scheduling first, as many of these bottlenecks will disappear with careful scheduling.
So just like the previous example, we end up working on a problem that does not increase the overall flow of product through the plant, and we see minimal results from our efforts.
Why These Methods Don't Work
The issues that arise with implementing lean as described above are:
If you improve an area that is not a constraint, all you end up doing is building WIP. The WIP piles up because the constraint operations in other areas cannot process it fast enough, tying up capital and creating waste. To add insult to injury, your work force will see all that wip building and slow down, draining efficiency.
The opposite occurs on the back side of the constraint. Workers see they have no work in front of them, so they slow down to "make their work last". We generally punish our workers for standing around doing nothing, which reinforces this dynamic.
Another problem can be that the process was greatly improved, but it's effect on the overall plant are non-existent but utilization of that process is so low. Removing 20 hours of process time from a plant with 20,000 hours of work monthly will not provide noticeable improvements.
All of these can be overcome, but you need a great deal of discipline as an organization. Almost every organization claims they possess this, but almost none actually do initially. You need a dynamic scheduling and planning system in place that measures capacity at each station, moves work or workers around based on actual work present, and follow up to make sure this occurs. We will be presenting the outline of such a system in an article later this summer.
Where Should You Start Implementing Lean?
The answer should be obvious at this point. I firmly believe that focusing your efforts on your constraints is the ONLY way you will fundamentally change your business. This can be painful at first, with lots of mistakes and growing pains. You need to have a little patience and be willing to spend extra time and training to make it work. But ultimately it is worth it.
If you succeed at removing the constraint, you won't have to convince anyone that improvements were made, the results will come relatively quickly and be dramatic:
- More throughput in the plant
- Efficiency will jump noticeably
- Potential improvements to quality and safety
- WIP will be gone, or in different locations
- The people on the shop floor will know that positive change has occurred, and will feel they created it
Tips For Implementation
Spend a lot of time offline choosing the constraint to tackle. Apply real problem solving techniques to the situation. Dig deep measuring tact time for internal customers and all the dynamics effecting area.
I prefer the Operational Excellence model for addressing constraints as opposed to the Kaizen model. There are a number of reasons for this which we detail in our Operational Excellence vs Kaizen article, the most important of which is simply giving yourself enough events to dig deeply into the problem and actually change your business.
Include safety and quality throughout the process, as well as a majority contingent from the shop floor (including people who work in the process, supply the process, and are customers of the process)
Include the supervisor or lead that is in charge of the area. They need to take ownership of the improvements.
You will probably have a number of events to tackle the key elements of the improvement, which will include: data collection, process improvement, standard work, 5S, maintenance, scheduling, safety, and quality.
Spend some time analyzing what will happen after the constraint is freed, and try to address potential issues before going live. For example, you may find that you many not have adequate material handling and need to rent a fork truck until another one can be purchased.
Conclusion
Some people in the lean industry have strongly disagreed my assessment in the past, arguing for a culture building approach of small, easy events followed by bigger events as the plant matures. While I strongly believe in building culture, most senior company leadership will not want to keep investing money on culture alone with seeing some tangible results to the bottom like. Focusing on your constraints will deliver results, while also building a lean culture through success.