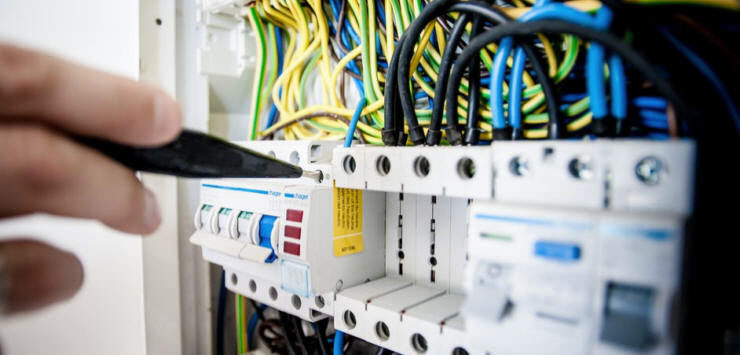
How many maintenance electricians are masters at 8D? How many regularly practice 5 whys? How many know what an A3 even is? Very few have these skills from my experience.
Electricians usually have little formal problem solving training, yet every single day they accurately solve and find the root cause of some of the most complex problems in your plant. So how do they do it, and what can you learn from them?
Too often as leaders we become enamored with the tools we use and forget the underlying reasons we use those tools. Problem solving tools like A3s exist for one reason only; to force us to use a disciplined approach when solving the problem and not just to conclusions before we properly have vetted the potential causes. That's ultimately it. Electricians are forced to use a disciplined approach to problem solving due to the nature of their work. Learn from them and apply a similar disciplined approach when solving your daily problems.
1) Define the Problem
For electricians, this is very easy. A piece of equipment is broken down and won't power up, or some feature is not working as it should. Someone wrote up a work request, and they verify that the equipment does not actually work.
This step is equally important to a manager. It often seems trivial, but we need to clearly state what the problem is, then go out and verify that it is indeed the problem.
2) Come in with no Assumptions
This will sometimes trip up an electrician as the will assume they already know what the problem is. Maybe it is a fuse that keeps blowing, but rather than simply replacing the fuse, a good electrician will ask why the fuse blew and look for other problems.
Just like the electrician, we need to keep an open mind and avoid assumptions. For example, several years ago my plant received a complaint from a customer that a product in the field did not match the drawings. Field service immediately determined that the contractor had assembled it wrong in the field, while the quality department in the plant surmised that it was manufactured wrong. I had to stop them both and make them take a step back from these assumptions. Later after a full investigation it was determined that neither group was right, that in fact the customer did not have the most current set of drawings. Any corrective actions taken based on the first set of hasty conclusions first drawn would have not solved the problem or prevented it from occurring again.
3) Measure
Electricians use their multimeters to check voltage at key points in the system. The operator of the machine may tell them there is no power present, but the electrician can't assume that for safety reasons and must check for himself.
As leaders, we should also be measuring and taking data to build a true picture of what is occurring in our throughout problem system. Don't accept what you are being told, get hard data and know for sure.
4) Follow the Schematic
Electrical schematics are critical to troubleshooting electrical problems. The electrician starts at the beginning of the circuit, tests it a key junctions, and follows every path that current travels in the circuit. Eventually, after testing many components and following many lines of the ladder, a route cause is found. Sometimes, the process may have to be repeated as the failure may have taken out multiple components.
When solving problems, we should be taking a similar approach. We should be using process or value stream maps to step through the problem process. We should test ALL branches to determine the problem, and don't assume that it is one factor alone that caused the problem. It is far too easy to quit when we find the first possible cause, but be disciplined and find ALL the possible causes.
5) Verify
After the equipment is fixed, the electrician will have the operator start the machine and verify it's operation.
We need to do the same thing. Verify that the problem has indeed by resolved and audit as necessary; Inspect what you Expect.
That's it. Most problem solving systems offer a much more complex and complete methodology, but sometimes I find it useful to simply things and think like an electrician.