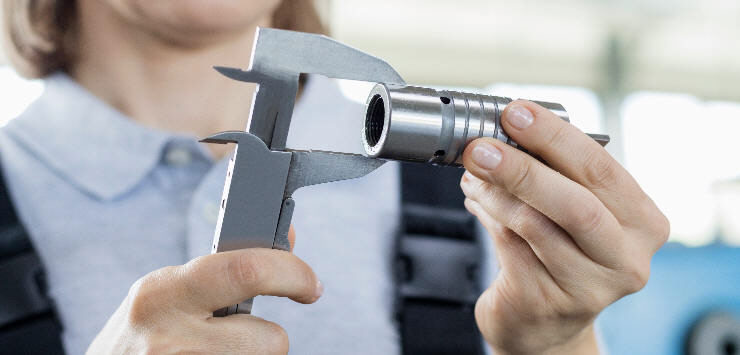
Quality management in job shop can be extremely challenging due to variability found in high-mix low-volume environment. Every day offers a new challenge, yet we need continually improve our quality without stifling productivity. The responsibility for quality lies not only within your quality department, but with your entire organization as a whole. Here are a few solutions to the common challenges we face each day.
What is Critical To Quality (CTQ) on the product?
When each item is different, and potentially is for a different customer, what quality specifications does the customer really care about? What is Critial to Quality for them? Obvious general standards such as AWS, ASTM, or others will always apply, but often there will be industry specific and customer specific which will not be readily apparent to operators or quality assurance.
The answer to this is obvious, better communication, but how is this accomplished? Here are some steps you can take:
Make sure your sales force and order entry mechanisms, whether that is a website or customer representative, properly document and transfer quality considerations. You may wish to provide them with additional training so they understand what key questions to ask. A standardized form for them to document critical to quality standards is also very useful.
Research industry-specific standards for individual customers in industries new to you. Medical, aerospace, defense, structural steel, and many other industries have some commonly accepted standards. This may seem redundant when you are already asking the customer, but people tend to have a narrow world view and often "assume" you know about their industry's standards or simply forget to mention them. You can then follow up with the customer on any potential issues you uncover.
Ensure language translations are done correctly if you are doing work for customers in other countries. Often it is not enough for the translator to know the language, but they also should have an applicable technical background as well. Keep in mind differences in culture, measuring systems, or even how dates are recorded. A recent client of mine had a very unhappy customer when the delivered product on May 2, 2019 (5-2-2019), when their German customer was expecting Feb 5, 2019 (5.2.2019).
If you are using engineering drawings, make sure this information is on the drawings or part of the drawing package. Critical tolerances should be highlighted in a manner that no one can miss them, such as using larger fonts or red highlighting. If special testing requirements exist, they also need to be included in the drawing package. Areas with special tolerances or testing requirements should be readable by quality and production, so you may wish to offer expanded views of these areas.
The drawings also need to be consistent from job to job, and between different modelers and drafters. Put quality notes in the same place on drawings, render them the same way, and with the same markings on each set produced. This consistency will help shop floor operators and quality personnel immensely.
The information must be readily available to shop floor employees and quality, in the location work is being done. Having them tucked away in an engineering or supervisor office will help no one. Senior plant management may want to highlight critical specifications with supervisors verbally and via written reminders. In an environment that is constantly changing, you will have to re-enforce critical messages multiple times, using multiple delivery methods, or the message tends to get lost in the noise.
Follow up with the customer after the project is complete, and get feedback on quality issues that occurred. Some companies assume that the customer will complain if there are issues - don't. According to some studies, 96% of customers unhappy with quality will not complain, but simply take their business elsewhere. While these numbers may not be as high in your specific industry, you should assume a large amount of your quality issues will go unreported. Let the customer know that quality is actually important to you, and that you will use any issues as an opportunity to improve.
Over processing
This is extremely common, and ties back to knowing what is critical to quality. Operators will apply more stringent standards than what is required by the customer, and do extra processing to obtain a finish than what is required. The same is true of quality inspectors, who will hold product to much tighter tolerances than what is required. Superior quality is great, but only if the customer finds value in it and is willing to pay for it.
For example, in a previous plant I managed we build rebar foundations that were embedded in concrete. These products had large welded segmented rings that held the product together. Our corporate quality office began to aggressively control the weld quality (appearance) and material grade used in these rings, adding a large expense to each item. The problem was that the rings were simply used to hold the product shape in transport, and once concrete was poured, the rings were literally thrown away. In this case the customer was not willing to pay for the additional quality.
Waiting
Waiting is another common issue, and is caused by the disjointed nature with which production occurs in a made-to-order environment. Production will be completed, and often resources are tied up for minutes or even hours waiting for inspectors to arrive and complete their work. Some of the tools you can use to minimize include:
The inspection process should be removed from the flow of the value stream whenever possible. For machine operations running batches of product, this is often accomplished by providing a designated quality inspection area where inspection occurs. This scenario is far from ideal as you are potentially adding additional transport waste and will add to the overall lead time, but it is preferable to having operators standing around waiting for inspection. Inspection sampling while the batch is running is preferable but not always feasible, depending upon your product.
For fabrication and assembly operations, is possible set up multiple stations leaving one idle. Work is completed on a product in one station, and workers then transfer over to the next workstation to begin work on the next product. Inspection can then occur when available, material handlers remove the finished product, and the next one is staged. This eliminates the waste for not only inspection time but also material handling.
Get all the information you need before inspection begins. Often critical information is missing and needs to be obtained mid-inspection. This is unacceptable and really a symptom of poor planning.
Andon tools such as stack lights or flags can be very useful to visually show what product needs to be inspected. Inspectors are often forced to work between various stations within a department, or even throughout the plant, and may walk right by completed product not knowing it requires inspection.
Quality inspection can be a constraint, and we should use the same tools we use to manage production constraints and bottlenecks to control this lost time. The process time of inspecting product varies in job shop, just like the production time does. Thus, it is critical for quality personnel to be part of production planning process. Product that requires longer or unique inspection should be managed via product mix control charts, and minimized by shifting the production schedule just like you would for any other constraint. It is also conceivable that in some instances you set up a drum-buffer-rope system for inspection.
You should have standard work for inspectors, just like any position on the floor, and it should be audited by quality leadership. Just like with production standard work, it should be focused on processes as opposed to specific product as your product is constantly changing.
Insufficient tooling, equipment, processes to do the job
So you have all the information you need to produce the product, quality is on board and has the proper control systems are put in place, and when it gets to the shop floor you find out you cannot produce that level of quality with the equipment you have.
Your organization needs to track not only the sizes and capacities of your equipment, but also the expected quality. Poorly maintained 50 year old lathes with bad bearings and loose tolerances are never going to be able to produce world class aerospace products. Air bending (no bottom die) on thick steel cannot produce precise bends when the process itself has an inherent 5% error rate due to material inconsistencies.
The bare minimum your organization needs is a regularly updated Matrix which describes quality capabilities by process, or even
by machine. This could be added to an existing capacity matrix or be a stand alone document. This information
needs to be available to sales and engineering, and be used in the bidding and engineering process.
However, this many not be enough. You will need people on the front end of your operation with a deep understanding of your processes your company uses and potential secondary quality issues that arise. For example, welding a thick machined block to gauge sheet metal may be cause severe warping, or may be the product is fine in production, but there is no way to ship without damaging it.
This is why your organization needs to have pre-project meetings and reviews with the shop floor experts to try to minimize these issues before they happen.
Difficulty In Implementing SPC and other Six Sigma tools
I am going to just briefly touch on this here, and write a full length article about it at a later date. SPC stands for Statistical PROCESS Control, not Statistical PRODUCT Control. It is a difference in philosophy that cripples many job shops because they assume because they have small batch sizes, no Six Sigma tool applies.
Six Sigma is about managing your process, not your products. Just like lean, the tools can be applied, they just look "different". For example, you may not be able to directly chart small batches of machined parts that vary between 2" to 5" length. However, if the tolerances on said parts is all the same, you could ignore the overall size and just chart the variation on each part, which would give you useful control data.
Conclusion
These are just a few of the issues that one must face when managing quality in job shop. If you see a lot of parallels between implementing continuous improvement and improving quality, you are right. Improving your quality to world class can be achieved if you are willing to think outside the box, do your homework, and implement systems to limit the negative effects of your variability.