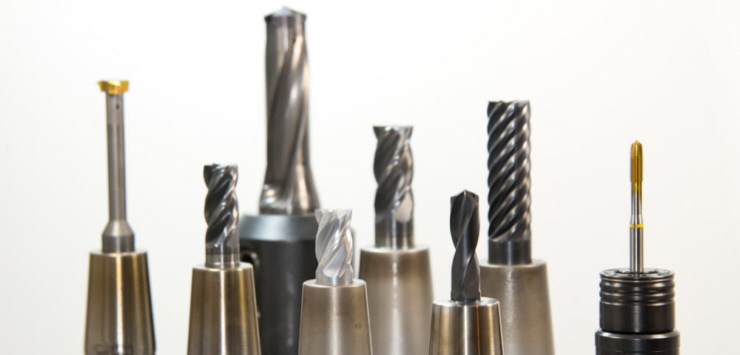
One of the most powerful lean tools you can apply in a job shop is Single Minute Exchange of Dies, also referred to as quick changeover. Because process times, routings, and work load vary greatly, it is imperative that your shop is flexible and has the ability to change over to the next job very quickly and efficiently. SMED is the basis for this transformation, so let's get started examining it's key elements.
What is SMED?
Single minute exchange of dies means transforming the process of changing over between jobs so that it can be done extremely fast. It involves removing as much waste from the process of changeover, and redesigning your entire process so that much of the changeover can be done while the machine is running (offline).
Benefits in a Job Shop
The key benefits of SMED in a job shop include:
- Reduced changeover times improve plant efficiency
- Flexibility to run small batches
- Meet rush customer orders by being able to quickly retool to meet demand
- Standardizing the changeover process helps prevent machine damage and increases quality by ensuring the first part run will be correct
Implementing SMED
The basic steps for implementing SMED are:
1) Choose a Valid process
If you've read some of my othe articles, you can probably guess where I am going with this. The Theory of Constraints should be the framework for your improvement activities, and thus it would be wise to focus your SMED efforts in a constraint area.
Also be sure that the area in question will significantly benefit from the improvement effort. If the changeover only takes 30 seconds and you run the process 8 hours on average between changeovers, you would be wise to focus your efforts elsewhere. Changeovers should take a significant amount of time and/or happen frequently.
2) Identify Steps in the Changeover
Break down all the keys steps in the changeover process. Include all steps that the workers in the area must do, and any the machine must do. For example, between jobs in may be necessary to calibrate a machine or run a cleaning cycle; this should be included to the steps. Also, make sure to include things like scrap removal, operator PM's, loading programs, changing consumables, or any other functions that is required to be performed before you run the next job.
3) Remove External Steps
There will be steps that absolutely have to be done while the machine is down - those are internal steps. But there will be steps that can be done "offline" while the machine is running - these are external steps. The ultimate goal of SMED is to transfer as many of these as possible to external steps. Often this requires you to redesign the work process, and possibly redesign the tooling or machine itself.
4) Apply Lean Principals
On the remaining internal steps, apply lean tools and principals to optimize them. Common tools employed can include identifying the 8 wastes, 5S, and standard work.
Examples
Don't be fooled by the name - SMED principles can be applied to nearly any process - not just presses and machine tooling. The ultimate example of SMED in practice is a pit crew in auto racing changing 4 tires on a car in 20 seconds, a process that would take your average car owner an hour to do. So here are a few examples of SMED in industry:
Plasma Table
Plasma tables have consumables that control the flow of gas and burn out as they are used. These consumables also may need to be changed when cutting thicker steel. The process of changing consumables can take as long as 15 minutes each time it is performed. However, if you pre-assemble the consumables offline and bring them over as part of a complete package and have the proper tools and gauges at the point of use, that can be dropped to a few minutes.
Another example from a plasma unit is the table "grates" that the product sits on. This grates are and burned as a normal part of the cutting process and eventually have to be replaced. The table often has to be shut down for an extended period while these grates are replaced. Build extra table trays and build them offline, and replace them as a complete unit. If you have multiple cutting tables on a unit, you should never even have to shut the machine down at all to replace these.
![]()
Weld Wire
Often weld shops must frequently switch between weld wire and possibly weld shield gas to weld different materials. This can involve replace a roll of wire, feeding it through the machine, and changing the regulator to a different tank of gas. This can be nearly eliminated by retooling. External dual-feed welders such as the one shown below allow you to change gases and wire simply by pressing a few buttons and grabbing the other gun, reducing a process that would take 15 minutes down to a few seconds.
![]()
Printing Press
Older Beilomatik printing presses were used to print and produce spiral bound notebooks. Often it would take up to 24 hours to reset all the thousands of moving parts and sensors for a new sized job. Quick change tooling was developed where you could lift out sections of the machine and tooling, and replace them with sections you setup offline for the new job. This brought changeover times down to 4 hours instead of a full day.
Another printing example is on-the-fly roll splicing. The machine often has to be shut down for an extended period of time when a new roll of paper is put on, and possibly re-thread the web through the machine. With on-the-fly spicing, the back end of the machine has multiple stations to position rolls of paper which can be put on and taped to splice offline. When it is time to change rolls, the machine speed is drastically slowed, a splice button pressed and it is automatically attached to the web running through the machine while cutting the old roll of paper. The splice is then slowly run through the machine, the splice area cut out after sheeting later on in the process, and then returned to full speed operation.
![]()
Shot Blast Machines
Shot peen blasting use large motors with wheels throw shot "BB's" at metal to blast away mill-scale, slag, rust, and other imperfections. These wheels are considered a consumable and must be replaced often. Replacement used to involve replacing all the individual components, re-timing the wheel so it shot directly at the product, testing and adjusting as necessary. One of the greatest improvements made in this process involves wheels where the blades and impeller can be quickly removed and replaced. The units are also pre-timed, so you don't have to adjust timing each time you replace this components.
![]()
Fabrication Tool Carts
Often in machine building and fabrication industries, machine sizes and tool requirement vary from job-to-job. So instead of having all your tools you could possible need on a shadow board along a wall, often it is best to make your tools mobile. Build tool carts with the tools you use 80% of the time on the carts, and put the more obscure ones along the wall. If you are building from engineered drawings, put a slanted top on the table so the worker has a place to put drawing packages. So once a project is done, the worker can simply roll his work station over to the next machine to work on, or move it out of the way to await new work.
![]()
Machining
The most common example of SMED would be the automatic tool changer, which contains many of the common tools needed and simply require you to switch tools on the CNC control. They do have their limitations, however, as they only have a limited number of slots for tools and will need to be changed out from time-to-time.
Another example is fixturing. Often fixtures need to be set up each time a new part is machined. However, many machines can be set up so that fixture can be set up for the next part offline, then the entire fixture set in place when ready to run. Keep in mind these fixtures should be set up to simply drop in without adjustment or shimming. Build the system so it is robust so that accounts for accuracy to the operator does not have to do so each time they re-fixture.
CNC machines are often prime candidates for standard work, as each operator does changeover tasks differently. Simply documenting the best current practice and implementing it uniformly at all work stations can yeild great results, and will eventually lead to even grean gains as you apply lean tools to them.
![]()
Conclusions
As you can see from these examples, Single Minute Exchange of Dies should be an integral part of your shop's plan to improve efficiency and lean out your operation. It provides the modern job shop with the flexibility and quick turnaround capabilities they need to service their customers in our ever evolving on-demand and just-in-time economy.