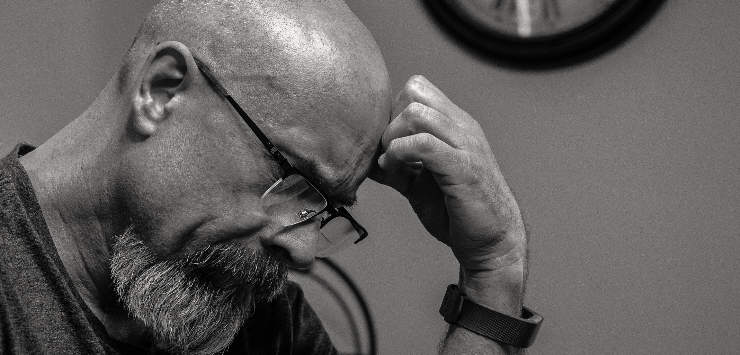
Everyone wants to jump right in and start the lean process on the shop floor, but is that a good idea? First you should ensure that your business is on solid ground and ready to begin the journey. Failure to do so will hinder your efforts and probably lead to failure. To use the American football analogy, first you need to learn to block and tackle. So before you start any continuous improvement program, below are some basic areas that should be addressed in your organization.
1) Accountability
This is probably the single most important thing you need to make sure is in place before you begin your lean adventure because without it you are doomed to fail. A lack of accountability is a cancer within your operation that will slowly destroy it from within, causing poor quality, slow delivery, and decreased profits. It will destroy moral and cause your best employees to lose interest or leave.
Accountability comes in many forms, including:
- Supervisors, managers, and senior leadership taking responsibility for their areas of control
- Workers accountable for the quantity, quality, and the safe manner with which they do work
- Good systems in place that hold people accountable
- Company as a whole is willing to take the actions that need to be taken, even if they are difficult, expensive, or unpopular.
The fastest way to change an organization is to start holding people accountable. Workers need to spend their time productively. Make those that create bad quality fix it. Make the right decisions, not the easy ones. Leaders that fail to hold people accountable need to be replaced. It is not always pleasant to think about, but absolutely critical to the long term health of your business.
So what happens if you start an improvement program in any functional area without accountability? Absolutely nothing. All your improvements will be wasted in an unproductive quagmire, or simply not implemented or sustained at all.
2) Quality
Almost all companies say quality is important to them, but often that is simply not the case. No one wants to make a bad product, but through the course of the entire process quality continually degrades. Bad quality can include:
- Passing bad quality on to external customers
- Passing bad quality between internal customers
- Inaccurate, incomplete, or late information
- Poorly engineered or tested products
- Incorrectly or poorly packaged items during shipping
- Damaged or inferior raw materials
Now I'm not implying that you need to successfully launch a complete Total Quality Management program before you start down your lean path, but you do need to have some basic systems in place to control it internally so it is not passed on to the customer.
When you first make quality a true priority, it will often be painful, with a great deal of push-back from both direct labor and various levels of management. But much like accountability, without it your lean efforts will not add value for the customer, which is a key tenant of the lean methodology.
3) Maintenance
A good maintenance program, even if only reactive to start, is the key to consistent performance in your organization. Often critical maintenance tasks are postponed or canceled because of expense or their negative effects on production. As the old saying goes, "Either decide when you will take your machines down for maintenance, or the machines will decide for you."
A basic maintenance program should include:
- spare parts for constraint or long lead-time equipment
- means to control parts inventories to ensure you have them when you need them
- basic PM program for both maintenance personnel and operators
- skilled technicians, some with specialty skills like logic controller. Their is more to modern maintenance than simply running a grease gun
- means to collect and interpret data
- discipline as a company to service equipment when it needs it
I know this sounds like a no-brainier, but I bet 25% of the business I visit don't take maintenance serious until there are catastrophic failures. They don't control their tool crib, monitor or control PMs, repairs are determined solely by cost, and generally they have no control over the maintenance function.
Without a good maintenance program, you will not realize lean gains because production will be wildly inconsistent and any data you collect skewed. Eventually you should strive to implement a (TPM) program in your plant as it will go hand-in-hand with your continuous improvement efforts, reduce costs, and allow your operation to maximize opportunities.
4) Scheduling and Planning
Scheduling is where I like to start all my job shop lean efforts. If you don't get the scheduling and planning portion under control, there will be so much "noise" that you will not be able to properly identify the real opportunities.
A good job shop scheduling system should include:
- Proper capacities down to the process
- System to monitor the backlog versus capacities
- A solid production tracker
- Dynamic Staffing
- SIOP alignment from sales through the plant
We have an entire series of articles detailing all these concepts and more in our scheduling section.
5) Leadership Support
This may be the hardest one to ensure on the list. Leadership will often claim to support lean initiatives, but when push comes to shove, in many organizations they do not. Much like quality and maintenance, continuous improvement activities are pushed to the side in favor of "making this month's numbers."
To make matters worse, lean may have been unsuccessfully implemented several times in a plant. This is very common in job shops where one size does not fit all, and lean practitioners need to be creative and modify the tools to the environment. Often the standard tools are applied without regards to the needs of a high variation, low run environment, they fail, and cast doubt on future opportunities. This creates skepticism about the effectiveness of lean in everyone in the plant.
Leadership must fully buy-in and be willing to do whatever it takes to properly implement lean, or it will fail - it is as simple as that. Otherwise when faced with priorities, improvement activities will always be secondary, and the difficult decisions and expenditures of resources will not be made.
Lean practitioners can help their cause by aiming small to start, and focusing on problems that matter to the company, and show some results. Nothing converts executives faster than a few good financial wins. Once you have a few quick wins that matter and have one over leadership, then begin to fully implement your program.
Conclusions
The most common response to this list is "We plan on implementing these with our continuous improve or lean programs." Wrong. If you don't have the self discipline as an organization to install this basic components now, what makes you think you will have the self discipline required to develop and sustain continuous improvement solutions? Most organizations in this position won't.
So learn to "Block and Tackle" first. These are business 101-level systems that will build a strong foundation for your future lean and improvement projects, and ensure your time and resources are not wasted.