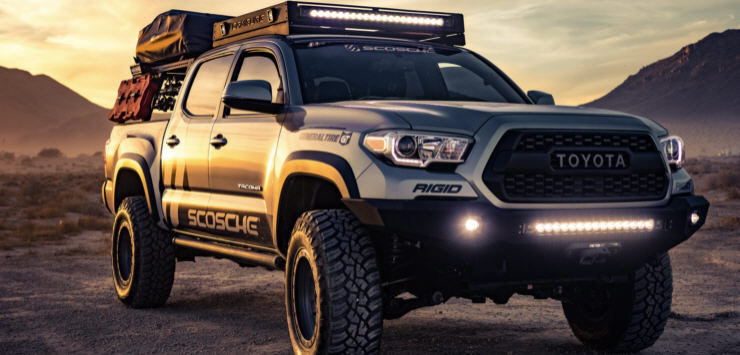
I don't care how Toyota does it. There, I said it. I just sent 90% of continuous improvement world into a frenzy. I can hear the comments now. "How dare you question the Toyota Production system, the greatest thing since sliced bread?" "Who are you to question their methods?"
Let me preface this by stating this article is in no way an article critical of Toyota. I have the utmost respect for the systems they have built and perfected over the years. Put simply, they have revolutionized manufacturing as we know it.
The Toyota Production System is the very best manufacturing system in the world - for manufacturing Toyota cars and trucks. Therein lies my problem - I don't manufacture Toyota cars and trucks. I run a job shop. I have product that weighs as little as 80 pounds, and as much as 80,000, all using the same equipment and running through the same value stream. My lead time varies from 2 hours to 2 weeks. Everything I build is custom engineered. In the end my schedule, product mix, process maps, and floor layout share very little with that of an auto plant.
So when a lean professional tries to use the same template and tools as used in conventional manufacturing, they fail miserably. At my last plant the first thing any consultant or continuous improvement manager would do is try to create a value stream map of the plant. I would tell them you better put a time stamp on that, because by noon tomorrow it is going to be outdated and all our bottlenecks will have moved. You will find similar issues with many of the standard tools used.
So ultimately my problem isn't with Toyota at all, but with "experts" and "consultants" who try to fit us all into the same bucket.
As most of you know well, we don't all fit.
We tend to ignore two very important lessons Toyota has taught us. The first is they took the work of earlier pioneers like Henry Ford, added their own experiences and innovations, and built a very efficient process to fit their company and product. Let me say that again, they built a process to fit their company and product. They did not copy someone else work verbatim and force feed it into their organizations, regardless if it fit. Yet unfortunately that is what happens in many organizations today, especially in organizations that don't fit the mass production model. Square peg, meet the round hole.
The second is Toyota was not afraid to challenge conventional wisdom and break the rules. Conventional wisdom of the time was that you ran as fast as possible, regardless of quality. Employee relations were adversarial at best. Waste was what you threw in a trash can. Wip was something a lion tamer at the circus used.
Today we are guilty of the same group think, but now Toyota is the conventional wisdom. All manufacturing has to be done the way Toyota does it, or it is "wrong". We need to have to courage to challenge these norms and find solutions that work for our business and product, just like Toyota did over half a century ago. We need to be willing to question everything; that is the only way true innovation can occur.
As Job Shop leaders we need to shop making excuses as to why we cannot implement lean programs in our plant, and instead have the courage to develop our own path. Success will not come easy and will require a much deeper understanding of waste and the continuous improvement process, but in the end is the only way your business can maintain a competitive edge.
In another 50 years, we may look back at another company that took what Ford and Toyota have taught us, added their own innovations, and redefined manufacturing yet again. Does your company have the courage to be that company, challenge industry norms, and not care how Toyota does it?