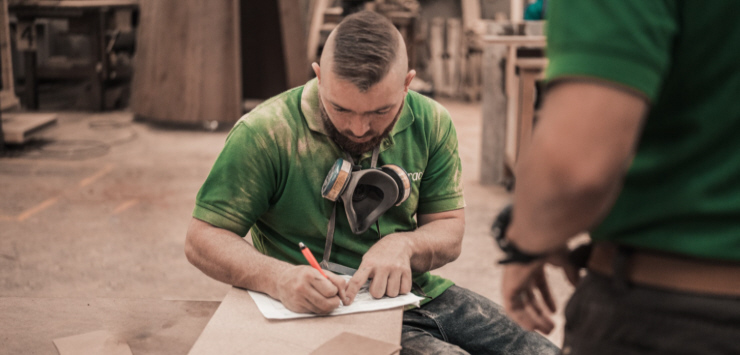
Cross training, also known as multiskilling, is something that is nice to have for most businesses. For a job shop, it is absolutely critical and one of the most important things you can do to improve the consistency and performance of your operation. So let's get started and explore some of the key elements of cross training.
Why Is Cross Training Important?
In a high-variation made-to-order environment, it is often impossible to level-load the production schedule so that every work station has the correct amount of work. Each customer and product requires a different routing through the plan, process times vary wildly, and unanticipated production issues are common as the job unfolds.
The solution is that your work force must be flexible, and you must be able to move both physical and human resources around the plant from areas of low demand to areas of high demand. The process of doing this is outline in our article on dynamic staffing.
Advantages
Some of the key advantages to having a cross-trained work force include:
Flexibility
As we discussed above, your work flow is rarely consistent and it will be necessary to move resources. While you may be able to move work to other
departments to alleviate the bottleneck, it is much easier and advisable to just be able to move the people.
Process Improvement
Any time you have a new set of eyes on an existing problem, you have an opportunity for new ideas and solutions. People from another department are outside the
existing paradigm and aren't afflicted with the most dangerous disease in a manufacturing plant, the "That's the way we've always done it" syndrome.
Contingency Planning
People get sick, have babies, and go on vacation. They unexpectedly quit for another job or sometimes retire. Don't allow your business to fall victim to
something that is a 100% certainty. People will be absent unexpectedly, so make that planning part of your business model. Production should not stop
just because Joe went fishing today.
Opportunities For Advancement
By creating a culture of cross training, you are creating more valuable employees who can grow with your business. You also have the ability to groom future
leaders who will have a wide range of skills in multiple areas of your operation
How To Properly Implement Cross Training
1) Identify The Critical Tasks
If you've read any of my other work, you know where this is going. First and foremost any process or job that is a constraint via the Theory of Constraints should have people cross-trained to perform. These take priority over all others and should be done as soon as possible.But it goes a lot deeper than that, you should train backups for ANY position that will become a constraint if the product mix changes or someone is absent. For example, you may have an isolated process that only has one machine operator. It is not normally a constraint. But what if the operator is gone for a week? A Month? Forever? See the problem with only having one person available to do the job?
Once you have constraints and potential constraints cross-trained, then go after all floor positions. Trust me, if you have a piece of equipment still in service on your shop floor, at some point you will want a backup for it.
2) Choose Employees To Cross Train
Be selective about how you cross train, at least at first. Choose employees with a willingness to learn and a willingness to work. Often you will have top performers who are looking for an opportunity for overtime. That opportunity may not exist in their department, but if you cross train them in another area it will be available to them. Cross training in this case is a reward for strong service. Annual reviews are a good place to identify those who are good cross training candidates.Also, you have a golden opportunity when people transfer to new jobs within a location. Make sure they are up-to-speed on everything in their current department before they transfer. This creates ready-made cross trained employees with little effort.
Eventually as your program expands you will train a much broader group of employees, and in fact in constraint areas you will want all employees cross trained in all functions.
3) Training
The biggest mistake that happens at this phase is that we as leaders undertrained. Simply having the candidate work with an experienced employee for a few hours does not make them cross trained, and in fact may cause more problems than it solves. The "cross-trained" employee many not be working safe, have low production, and poor quality. It is not their fault for this, but yours as a leader for not ensuring training was thorough enough.I recommend you put them through the training any new employee would go through, minus orientation and general skills. For example, if everyone can material handle with a fork lift, there is no reason to redo that training.
If time is constraint and you can't put employees through the full training, the bare minimum a cross trained employee should be able to do is:
Work safely - that is non-negotiable
Understand what a quality product is, and how to measure it
Be able to do the basic job functions on their own, without assistance. Actually run product, don't just watch. Most people learn by doing; simply watching won't be enough. This may be limited to one type of product and not everything the work cell is capable of.
Keep in mind, while you are doing training in any process, the capacity of the process will go down. As a rule of thumb, I always assume that you will earn 75% of the hours you would normally, for both people. So if you are working 10 hours shifts, you will only earn 7.5 hours during training, for both people combined. This applies to any training, not just cross training.
4) Develop A Training Matrix
You need a simple means to track progress with your program, so developing a training matrix is key. My Skills Training Matrix article goes into this process in detail.Training matrices require an incredible amount of work to set up and maintain, and what often seems like a simple process can take months or even years to set up. So my advice: Keep it simple. I start with a small matrix with a list of processes, and who is cross trained on each process. Have one for each shift and post it prominently. That's it. You can grow and expand it in the future as you go further down the lean journey.
5) Integrate the training program into your overall staffing and hiring plan
Potential candidates for cross training should be identified during the hiring process and noted as such in your overall staffing plan. For example, if you are a machine shop and you are hiring a lathe operator, someone who also has extensive welding experience in their past might be a good candidate for cross training down the line in a fabrication department in your plant.6) Keep skills current
Make sure to keep your workers skills current and have them work the jobs they are cross trained for. It may only be once a year, but as technology and processes changed, it is important to keep their skills current as well.