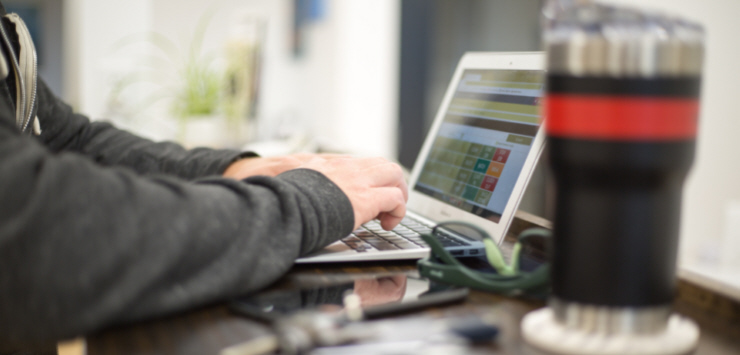
A training matrix (or training chart) is an integral part of your cross training program and the overall staffing plan. In its simplest form it is a chart showing the basic skill set of your work force, but can be expanded to be an integral part of your continuous improvement efforts. So let's explore them in more detail.
What is a Training Matrix?
A training matrix is a graphical representation of the current skills available and skills gap of your organization. It details each employee's current capabilities, and the capabilities the company requires in each area. There are two basic flavors for training matrices:
Skills Training Matrix
The skills training matrix graphically shows a chart of each employee, the skills and processes they are trained in, and the level to which they are trained. It might utilize a pie chart format to show skill level, or a numerical value. Some advanced systems will also track when the skill needs to be re-certified, and a link to any relevant documents such as training documents such as training checklists or job safety analysis (JSA) training sheets.The biggest benefits to a full skills matrix is that you will have detailed information on the skillset of your employees to drive training initiatives exactly where they are needed. Skills matrices are often expanded beyond simple job tasks and include quality, safety, and lean skills as well. They are present in the Gemba or work area for each department. They help drive a lean culture and promote growth within organizations.
The drawback to a full skill matrix is they are very time consuming to set up and maintain. It is not uncommon for HR to spend a year developing the initial matrix, and then having it fall by the wayside because on an inability to maintain it.
Cross Training Matrix
A Cross Training Matrix is actually more important to the long term success of your job shop than the skills matrix, but eventually you may want to do both. The cross training matrix shows who is trained for what process, and how many you need to have trained for that process. Even though you have backups at positions, you may want to have an "overflow" capacity built in where you can move extra people to elevate constraints as they appear in your plant.A very simple cross training matrix can be produced in an afternoon, and only takes a few minutes a week to maintain. It will not give you the wealth of information that a full skills matrix will have, but it will give you enough information to properly run your business.
A cross training matrix is absolutely essential to running your job shop; a skills matrix is a luxury. Decide how to best deploy your resources in your organization, and where you want to grow.
Build A Simple Cross Training Matrix
Take my advice, start with the simplest possible system, get it working, maintain it, then grow it over time. The most common reason for failing with a training matrix is trying to do too much, too soon. So start with the basic cross training program outline here , and build a simple matrix for it. The Microsoft Excel chart shown below is the absolute simplest system I have come up with, it works well, and will give you the bare minimum data you need to track cross training.
The matrix should contain the following information:
Date Updated
Shift
Department heading, with the key processes in each department
List ONLY the people that are cross trained for each process. Do not list the workers who regularly work there. Use the employees name and employee, not just employee number. This chart is made for people to easily read.
Behind each process name, put in parenthesis how many people you want cross trained. This will be adjusted as you travel down the lean journey, learn what your constraints are and how many people you need to elevate constraints when they appear. Read our theory of constraints and dynamic staffing articles for more details.
Any process where you do not have any backups, highlight the cell background red
Any process that does not have enough backups, highlight the cell yellow
Supervisors simply write in anyone they cross train for a job on the chart.
HR is in charge of maintaining the chart. They enter workers supervisors have cross trained. Anytime someone switches shifts, they are moved to another shift's sheet. Any time someone shifts to a new job within the plant, they are automatically added as a backup for the old job. New charts are printed weekly or monthly.
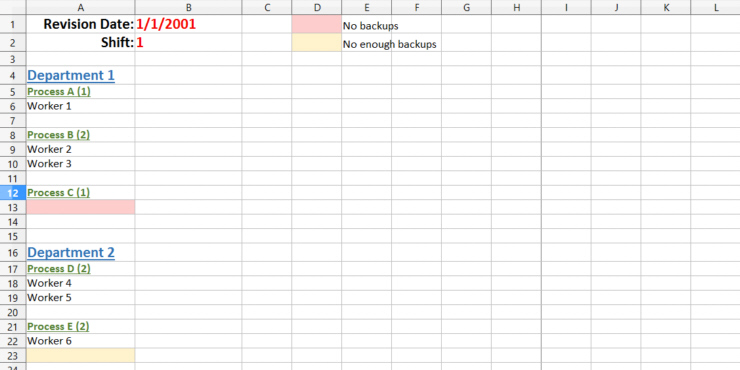
Download Cross Training Matrix Example - Excel file
In this example, process C in Department 1 has no backups. Process D does not have enough backups. You can see the gap in coverage instantly by looking at this chart.
I produced one of these charts for a small plant recently. It took me approximately 1 hr to compile the information, 1 hr to build the chart, and HR approximately 5 minutes to update it each month. It was posted in the office on the wall, by the supervisor's office.
Skills Matrix
The skills matrix is going to be a bit more advanced. Be prepared for a major investment in time if your organization is over 50 people. Also be prepared to build a system on the back end to upkeep it.
Word to the wise, my sure to limit the scope of your matrix. If left to grow organically, it will soon become diluted with an overload of information. For a plant of 300 people I once worked at, our training matrix filled a 10 ft x 6ft section of wall, printed in a 10pt font. It is often best to start your skills matrix at the department level, then replicate everywhere else. Scope it to the skills that are absolutely necessary, and add others later as necessary.
Start at the department level, particularly one that is a plant constraint. Add all critical processes to the matrix that are required to move production through that department. You may wish to also include other skills, such as lean or leadership potential at a later date. You also will want to add how many people are required for each process, and how many back-ups you would like.
Add all employee to the matrix, both full time and those that can be backups. List full-time employees first, and backups below them to get an accurate picture of your current staffing and the ability to scale your production.
Each employee will need to be rated on each skill based upon their level of competence. Some companies use 360 reviews or other techniques to find this info. For a manufacturing operation, I prefer just to start with training records and work through the supervisors and leads knowledge of the area. Not only will a complete picture unfold, but you will also find gaps in your training paperwork.
How you rate them is up to you. Many lean practitioners use the "pie chart" graph method, others use a simple numerical grade approach. I like to use a number rating, along with color coding on the chart. Here is my system:
- Blank cell = no aptitude for the skill
- 1. Basic skill level, can do part of the job - Red
- 2. Competent at the job, can most functions alone - Yellow
- 3. High level of competence, can do all functions - Green
- 4. High level plus has the ability to train others - Blue
Much like our other chart, we will label when the chart was updated and what area it covers. Below is an example in excel:
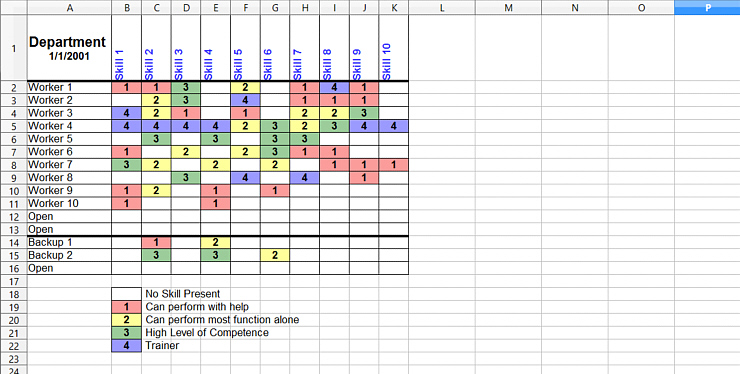
Download Skills Training Matrix Example - Excel file
This chart provides a simple visual representation of the skill levels of your department. Each employee and skill can easily be cross referenced to determine holes in your departments skills. Each cell labeled open means that is a position that needs to be filled per your staffing plan.
Once you complete one department, post it in that department as part of your visual workplace program. Replicate the chart throughout all departments, and develop a system to keep the information updated. Usually it will be a combination of HR and supervisor reviews that will provide the updated information, but you may all get input from the safety, quality, and continuous improvement departments as well.