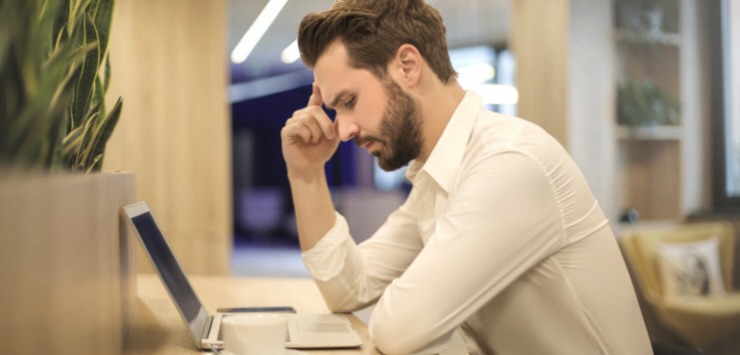
Root Cause Analysis is a systematic approach to finding the underlying cause of a problem, and developing a solution to prevent if from occurring again. It has roots in Total Quality Management, and is a core principle of lean and an integral part of the continuous improvement process.
We use root cause analysis in our everyday lives and probably don't even realize it. When you go to a dentist with a toothache, you want the dentist to find the root cause of what is causing the problem. If we have a leak in an upstairs bathroom and call a plumber, we want the plumber to find and fix the leak, which is the root cause.
However, when attempting to solve problems in our workplace, people often don't do their due diligence and jump to answer the question before properly researching the reason why something happened. In our plumber example, what if the plumber simply replaced the first piece of pipe he found without checking the whole system. Then next week it start leaking again, we call the plumber in again, and this time he replaces a different pipe. Another week passes, and again we have a leak. The plumber is called again, and this time they find the real root cause, which was a broken seal around a faucet which allowed water to run down the pipes, and leak onto the floor. Would we be happy in that scenario? Would we use that plumber again? Probably not. Now imagine how your customers feel when we do the same to them with incorrect shipments, late deliveries, and poor quality.
In job shops it can sometimes be even more difficult to find the true root cause of a problem as product and processes are constantly changing. It is critical that a systematic approach is used to uncover the truth.
Root Cause Analysis Basics
Six Sigma offers us a great framework for conducting our analysis using the DMIAC methodology. DMAIC stands for Define, Measure, Analyze, Improve, and control. For more info and DMIAC, look for my article on it coming soon.
1) Define the Problem
This simple yet often overlooked step. What exactly is the problem? How does it align with customer needs? What are the symptoms and issues you observed? What happens if you do not solve the problem - what are the costs?
2) Measure and Collect Data
Any analysis of the problem should be data-driven with as many unique sources of information as possible, including:
- Is it measurable? What critical KPI or Critical To Customer metric is affected?
- Machine data, video, and any other evidence available
- Customer and worker feedback
- Review records - has this problem happened before, is it repeating?
3) Analyze the Data and Identify The True Root Cause
It is critical that we did deep and ask critical questions about what is really occurring in our plant. It is very easy to find symptoms of the problem and "assume" they are the cause. Don't be fooled. You will know when you found the real root cause because there will be concrete cause and effect evidence, and you will not be able to break it down further into other causes. Also, don't assume there will only be ONE root cause, as often there were be multiple causes contributing to the problem.For example, if you hear a noise coming from your front left wheel on your car, it is easy to assume it is a tire problem. We examine the tire, the wear is fine, in balance, and in alignment. So we take it off and look at the brakes. They rotor and pads are not excessively worn, and rotor is not warped. So we pull off the wheel hub, and the wheel bearing is broken and ball bearings literally roll out on the ground. It would be easy to stop there and assume that is the problem, but if we looked a step further, we would see the lower ball joint is also bad, and also contributed to the noise.
I like to start any root cause analysis by asking the simple question "What Has Changed?" A system may be working efficiently, and a change to material, people, or process occurs, and a problem results. Also, sometimes the change itself isn't the problem, but how the rest of the system interacts with it is.
When trying to identify a root cause it is important to ask HOW or WHY the problem occurred, not WHO. The point of root cause analysis is to find the solution so it doesn't happen again, not assign blame.
It is also important to remember that while we need to find the root cause, we can't ignore the symptoms in the short term. For example, if your house is burning down, we want the fire department to put out the fire first before starting the investigation into how it started.
Lean provides us some standard tools to help us drive down to find the true root cause, which include:
Change Analysis
Change analysis is the most common tool I use when doing root cause analysis in a job shop. The environment is constantly changing, so changes in process, environment, people, and product are usually the leading cause of problems.Fishbone Diagram
A Fishbone or Ishikawa Diagram is a simple graphic representation of the problem where we attempt break down cause and effect.5 Whys
Keep asking the question why until we can no longer dig any deeper, usually 5 levels deep.Barrier Analysis
This techniques looks at what barriers were in place to prevent the problem, and what may have failed. For example, let's say we passed bad quality on to the customer, even though the product was inspected by quality control. We would examine how the product made it through the quality hold point undetected.We've also added our own unique take on problem solving with, Solving Problems Like an Electrician that you also might find useful.
4) Improve systems to Prevent the Problem from Reoccurring
Often there will be more than one solution to prevent the problem from occurring again. These could include:
- Design changes
- Process changes
- New materials
- Quality checks
- New procedures, work instructions, or standard work
- Training
- Equipment repairs, refurbishing, or Total Productive Maintenance (TPM)
- New Technology
- Environment changes
Along with the fix for the problem, make sure to create an action item tracker that determines who is responsible for what activities, and when they need to be completed.
5) Control the system to verify it is fixed, and stays fixed
As a former boss of mine always said, "Inspect What You Expect". What gets audited gets done. Once your corrective action is complete, you must ensure compliance with the new procedure or process, and ensure that things don't slide back to "The way we have always done it".
Positive Note
Keep in mind, Root Cause Analysis is not only for solve problems, but also reconstructing successes. If you think about it, when competitors deconstruct and examine a successful competitors product, that is exactly what they are doing, finding the root causes of why it is successful.
So don't be afraid to examine the things working in your organization too, find out why they are successful, and how you can replicate those success throughout your organization.