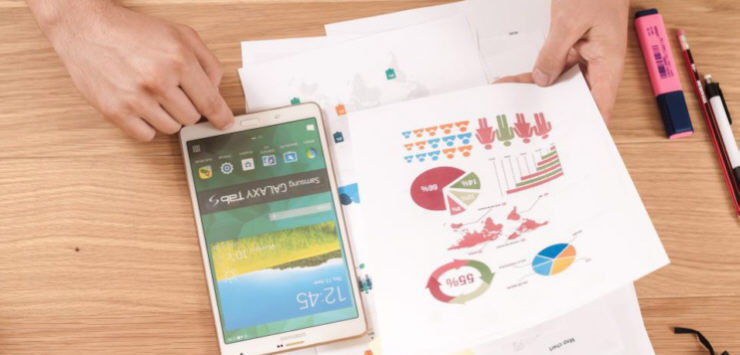
The most common question I am asked is something similar to this: "I have lean experience, but I work in this chaotic job shop with different routings and process times, and I don't know where to start." My response to this is simply "You've answered your own question. If you feel your shop is chaotic, you need to get that under control, and you do that by improving your scheduling process."
Heijunka is the Japanese word meaning "leveling." Getting your schedule under control in a job shop really implies one thing: developing systems to level your product mix and variation. This article is an overview of that process meant to "bring It all together", and will the reference various resources needed to accomplish this. Also, consider it a "living document" that will grow as more resources become available. So let's get started.
1) Plant Capacity
The first thing that should be calculated is the overall plant capacity. Almost all job shops have this done already, but very few of them do it right. It is assumed that most shops will be running a series of jobs with estimates (in hours) associated with them, and so you will want to have a plant capacity in hours as well. There are a number of factors which need to be added into this calculation which are often not considered.
Associated Article(s): Capacity Planning
2) Capacity By Process
Next, calculate your capacity in each department and each work station in hours. This will be at the heart of controlling our mix, and is one of the most critical steps of the process.
Associated Article(s): Capacity by Process
3) Indepth Production Tracking
If you don't have a production tracker, you should have one. Even if you do have one, you need to make sure you include all steps of the process, including support functions (engineering, materials, programming, ect). It should also list all your process steps in it, and have completion dates/times so you can identify problems early in production, as opposed at the end. The Gantt Production Tracker article presents several simple models that can be produced in Microsoft Excel.
Associated Article(s): Gantt Production Tracker
4) Compare Backlog to Capacities
This is where the rubber meets the road so to speak. We need to develop a process where we compare the jobs in our backlog against our plant process capacities. This will provide the core data we need to make decisions for our plant.
We will need at least two type of charts. The first will be a simple comparison of the hours assigned to each job, each day, in our back log versus process capacity. The second should be a chart of the same data but in another format, such as pieces or inches run? Why do we need two type of charts? One will tell you the quanity of work, and the other will tell you the nature of the work. We need both sets of data to be able to make good decisions.
Associated Article(s):The Two Dimensial Scheduling Problem (why you need both charts)
5) Play Tetris With Your Schedule
For those of you not familiar with the game Tetris, it was a simple game from the early 1990's where various shaped blocks would drop down from the top of the screen, and you have to flip and move around the pieces to get them to "fit" with the pieces at the bottom.
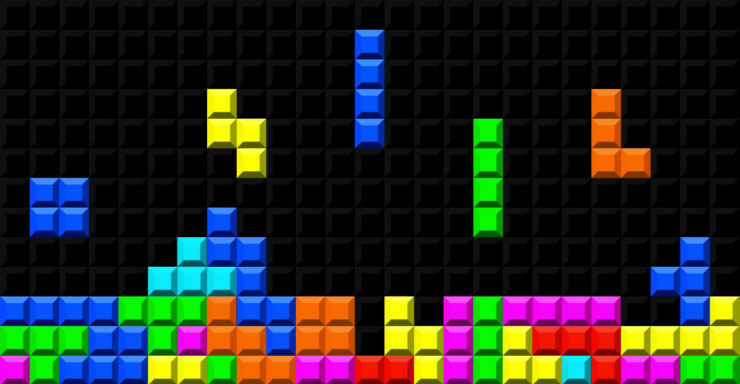
This is exactly what we need to do with our production schedule. We need to move complete jobs around the best that we can to get our schedule to match our individual process capacities. Some jobs may be moved up, so back (if possible), but in the end our schedule should be closer to being leveled for each process.
6) Dynamic Staffing
Develop a system to move people from processes that have excess labor to those that do not have enough. Doing so will control unnecessary working in progress (WIP) and help improve efficiency. To pull this off you will also need to master crosstraining and managing people's skills.
Associated Article(s):Control Work in Progress and Improve Efficiency Using Dynamic Staffing
Cross Traing (Coming Soon)
Skills Matrix (Coming Soon)
7) Make Tough Decisions
More than likely your schedule will still not be completely balanced and you will have to make tough decisions to get it closer to level loaded. Some of these decisions make be against convential lean wisdom such as adding inefficient labor or increasing WIP. However, these actions may be removing bottlenecks and possibly constraints, so the trade offs may be warranted. For example, you may wish to start part of a job early to peform functions that will be a future constraint, and hold those parts as WIP until needed at a future date. WIP and Inefficiency are not necessary bad if you are buying overall efficiency for your plant in the future with it.
Associated Article(s):
8) Scheduling is complete, But You Still Have An Unbalanced Schedule – Now What?
You've gone through the complete scheduling process, and no matter what you do, you cannot remove some bottlenecks. Then looking back historically, you see that this has happened a number of times in the past, and seems to happen where you get a certain mix of product. Congratulations, you've identified your plants real constraints.
Job Shops have varying process times and routings which lead to bottlenecks which move and change with the mix. If you can shuffle your schedule and eliminate these bottlenecks, they are not critical constraints. If, however, you cannot removing these bottlenecks with scheduling, and they will repeat in the future (not a one-off event), then these are the constraints that defining your business, and this is where you focus your lean efforts.
Associated Article(s):